
White Paper

Towards more sustainable data center
design using a CHP case study
​
White Paper 3
​
​
December 2021
​
EYP Mission Critical Facilities, Part of Ramboll (EYP MCF, Part of Ramboll)
Executive Summary
​
The primary focus of this white paper is to provide an example study that employs an on-site power and heating system to deliver GHG abatement and emissions reduction. The objective is to demonstrate how the data center carbon footprint and GHG emissions can be reduced by situating a data center next to a location where there is immediate need for campus cooling and heating.
The need is for onsite power production, achieved through the provision of a microgrid with utility power back-up, together with power efficiency improvement, achieved through heat harvesting and re-use. Utilizing CHP would result in GHG emission reduction of approximately 102,529 tons of carbon dioxide, 112.17 tons of sulfur dioxide and 49.74 tons of nitrogen oxides per annum. Heat recovery from energy production will also lead to an improved power usage effectiveness (PUE), of
approximately 1.1.
​
Content
​
-
Overview
-
Combined Power and Heating Systems for Data Centers
-
Heat Recovery and Re-used
-
Co-Generation Case Study
-
Data Center Power Usage Effectiveness (PUE)
-
Economics
-
Conclusion
​
​
​
​
​
​
1. Overview
​
The use of combined heat and power (CHP) systems is a serious and practical consideration for Green House Gas (GHG) reduction in the data center sector, taking its place amongst other initiatives which include a practical roadmap of progressive GHG abatement for existing data centers and net-zero GHG new data centers by 2030.
The use of CHP systems can provide energy efficiency and reliability improvements as well as economic and environmental benefits. While natural gas is not a sustainable resource, its use to fuel gas turbines for a CHP system providing both power and cooling for a 10MW data center could potentially result in a reduction of approximately 50% GHG emissions compared to the use of a fuel-oil fired system and utility power.
​
​
2. Combined Power and Heating Systems for Data Centers
​
Though data center loads have always presented an attractive profile for the use of CHP plants, few have been utilized. The reasons for the data center industry’s reluctance to install combined heat and power plants include the emphasis on short payback periods, and a lack of awareness of CHP systems.
Typical CHP system payback periods are in the region of 6+ years. However, the desired payback period for the data center industry is often 3-5 years. With this perspective, CHP plants are usually not considered for further analysis. Unpredictable IT loads and a tendency to under-utilize power systems has also contributed to the uncertainty. Facility operators are often left second-guessing the future and therefore are unable to adopt an informed approach to energy usage. Data center designers and operators are also often faced with challenge of low day-one data center demand, which contributes to making CHP systems less attractive.
The current and future demand for data center space, power and cooling presents the industry with new challenges including the need for increased power generation to meet this growing demand, and for sustainable design with smaller carbon footprint. Onsite microgrid power generation is likely to be a significant contributor to GHG abatement in the near future. Such generation will include renewable sources such as solar, wind power and fuel cell technologies. Utility power will typically be provided as a back-up as well as providing a source of power to support and energize systems in case a cold start for onsite generation is needed.
The ability to connect to the electric utility grid could also allow for the CHP to provide grid support services back to the utility, which can further improve the return on investment of the project. Careful consideration of plant capacity versus data center demand, combined with energy storage systems could allow the site to provide a range of grid support benefits to the electrical utility from regulation and spinning reserve voltage support to transmission, distribution, and generation upgrade deferral.
In developing countries, smart city and technology center designs ought to be sustainable through methods and means of utilizing all available energy at the site. In some countries, onsite generation is sometimes the only viable solution for reliable energy, but it can also present a lower GHG profile than incumbent energy from the grid. A CHP plant utilizing a cleaner primary source of energy, such as natural gas, versus the oil or coal burning generation plants typical of national grid systems in many countries will provide a means for reducing GHG.
Successful implementation of any CHP plant requires a careful analysis of the energy needs of the site. Fundamentally a load that can utilize the waste heat from the first pass energy conversion process is needed to achieve the conversion efficiency needed to make most projects financially viable.
​
​
3. Combined Power and Heating Systems for Data Centers
​
Heat harvesting can be broken into two categories for data center application:
-
High grade heat recovery (such as heat from CHP plant) and low-grade heat recovery such as from data center process and liquid cooling.
-
Low grade heat recovery, which can be conveniently and suitably applied to offset domestic water heating demand by pre-heating the water before the boiler or heating element.
Other applications that utilize low grade heat recovery includes pre-heating of air handling units air intake for administrative buildings, external frost protection, use in conjunction with heat pumps to provide higher grade heat and free cooling to the data center system.
Data center operations should consider using a data center process cooling system with processing fluid return temperatures at 98 degrees Fahrenheit (36.7°C) to raise domestic water temperature from 55-degree Fahrenheit (12.8°C) to 90 degrees Fahrenheit (32.2°C). This can result in significant energy savings for a campus application which requires constant flow of domestic hot water.
​
4. Co-generation Case Study
​
The efficiency of coal or fuel-oil based power plants is usually less than 35%. Typical natural gas generating plants have an efficiency from around 35% up to 47%. The rest of the energy from the power generation process is rejected into the atmosphere during power production phase. However, up to 65% of this waste energy can be recovered and utilized leading to an improved overall efficiency of the power production process. An additional benefit of locating power generation at the point of consumption is the reduction in losses associated with the transmission of power.
This paper presents a proposal for an improved power production process for data centers, utilizing heat recovery which can then be used for other applications such as heating water to high grade level and not limited to just low-grade systems. The design involves the use of CHP at the end user site, minimizing power transmission losses by capturing the heat from the exhaust of a gas turbine, thereby improving the overall efficiency of the power production process. Natural gas is used as the primary fuel source for the turbine. The installation of the heat recovery system boosts the efficiency of the plant from 35% to 80%.
​
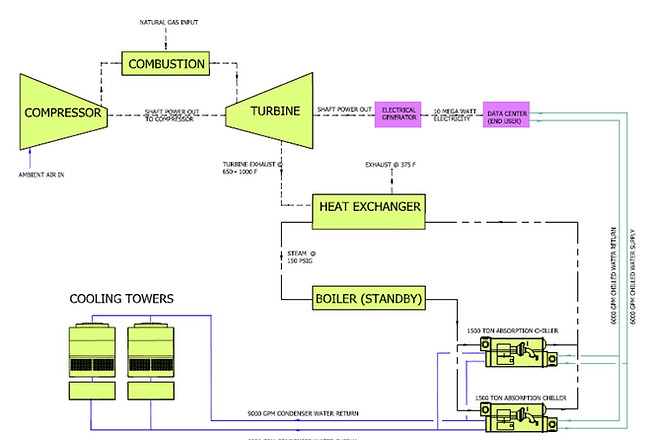
Figure 1 - Schematic flow diagram of a modified and improved power production plant.
The following examples are based on an assumed IT power capacity of 10MW (with overall electrical capacity of 11.48MW) and associated cooling demand of 3000-Ton (10.5 MW). A typical installation would include three turbine engines in a N+1 redundant configuration. All mechanical cooling equipment is also in N+1 configuration.
As indicated in Figure 1, the exhaust gas temperatures range between 650 degrees Fahrenheit (343°C) and 1000 degrees Fahrenheit (537°C). Exhaust gases are diverted through a heat exchanger to produce steam which can be used in an absorption chiller to produce chilled water. To control the pressure and the quality of the steam a boiler is provided downstream of the heat exchanger. The boiler will only be used if the steam demand is greater than that being produced by the heat exchanger.
In this design the estimated electric demand is 10MW, at full load operation using data published by Solar Turbine company, two 5MW gas turbines have a cumulative exhaust gas flow rate of approximately 150,000 lb/hr, sufficient to produce over 7000 Ton of cooling (24.6 MW).
Steam output can be estimated as.
Qsteam = Mexhaust x cpexhaust x (Texhaustfromturbine – Texhaustfromheatexchanger)
Where the Mexhaust mass flow rate, Mexhaust and temperature, Texhaustfromturbine are typically given as turbine performance specifications. The specific heat of natural gas exhaust cpexhaust is approximately 0.26 Btu/lb-F.
The following is the published gas turbine specification for Solar Turbine model number Taurus 60.
​

Figure 2 – Example of the Intermittent and Uncertain Characteristics of VRE - Source: Ela and others (2013)
The estimated 10MW computer equipment load will require a 3000 Ton of heat rejection. Traditional cooling systems frequently include a centrifugal chiller and cooling towers to reject the heat utilizing reversed Carnot cycle process. Typical cooling systems utilizing a water-cooled chilled water plant with centrifugal compressors, cooling towers and pumps have an energy usage range of 0.8 to 1.0 kW per Ton of cooling. Using 1.0 kW per Ton, the centrifugal chiller plant energy usage is approximately 3MW, leading to site total energy usage of 13MW (IT load plus mechanical load). Using absorption chillers, the additional 3 MW for the cooling system is removed from the proposed design thereby reducing demand and therefore the overall energy consumption of the facility.
Installing the co-generation plant at the site, will provide all required power, minimize power transmission losses, provide cooling and heating for both data center and the campus and, depending on the energy fuel mix, reduce the carbon footprint of the site. Also depending on the reliability of the grid, power reliability can be improved by onsite generation with utility power backup.
Figure 2 provides a summarized analysis using a theoretical calculator tool provided by the EPA Combined Heat and Power Partnership.

Figure 2 – Overall CHP Thermal performance.
Based on the above example, the co-generation projected displaced electricity production is 100,565 MWh/year which includes data center electric power demand, cooling load demand and reduced power transmission losses as summarized in Figure 3.

Figure 3 – Displaced Electricity Profile.
-
Estimated energy savings for this model is 29% an equivalent of the annual energy consumption of 7,664 cars or 3,759 homes as shown in Figure 4.

Figure 4 – Projected Energy Savings and Equivalent Energy Consumption.
Figure 5 provides a comparison schematic diagram for conventional power flow from a coal power plant and onsite power generation with heat recovery to meet cooling and heating demand load.
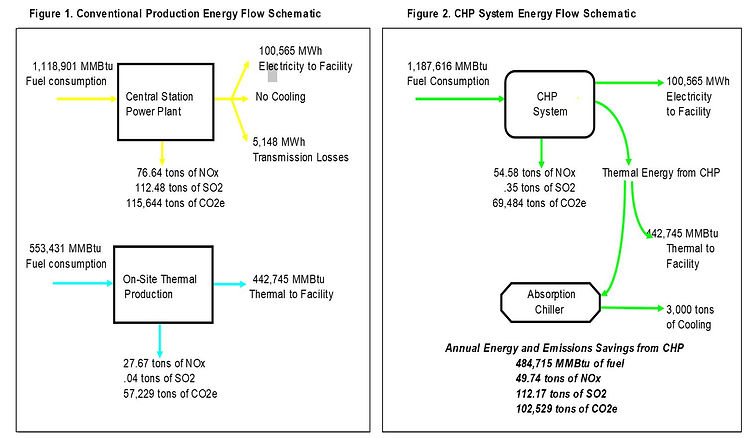
Figure 5 – Overall benefits of Co-generation power and cooling plant.
In this example, the design reduces the carbon footprint of a 11.48MW connected load data center by 50%, and fuel consumption is reduced by 553,431 MMBtu. The reduced carbon emissions are equivalent to total annual greenhouse gas emissions generated 20,258 cars or 10,818 homes. See Figure 6 below.

Figure 6 – Emissions Reduction Summary Table.
5. Data Center Power Usage Effectiveness (PUE)
​
Most of the power consumed by data center cooling systems is by mechanical refrigeration plant using compressors. In a centrifugal chiller plant like the one analyzed; the chiller power usage is approximately 0.546 kW/Ton. Co-generation plant will also lead to lower data center PUE since the chiller compressor power loads are reduced in the PUE calculation. In this case study there is reduction of 1638 kW of chiller compressor power for a 10MW data center with a total cooling demand of 3000-Ton. This leads to a reduced PUE of approximately 1.05.
​
6. Economics
​
Since the (US) natural gas industry was deregulated by the government, gas prices have until recently been falling. According to the Edison Power Company deregulation of electrical utilities may lead to slightly decreased electricity prices, making this onsite power generation a workable energy saving solution. The reluctance of private companies to adopt this type of solution is partly driven by unstable natural gas prices together with the initial capital outlay for the system. Government intervention and rebate programs will be required to encourage the participation of private companies. However, for Government data centers such as the projected modernization of the health care industry, this energy saving solution is a potential candidate.
In other parts of the world, such as Europe where 20% of the total electricity generation comes from Wind and Solar, doubling the world average share (9%). Although this is an incredible number, the region is still dependent on Natural gas (24%) to reduce the consumption of Coal and to meet the increased energy demand and storage, especially during the winter cold months.
​
7. Conclusion
​
As the research continues for alternative energy sources, the efficiency of the existing power plant cannot be ignored. Improvement of existing power plants and designing systems with heat recovery will not only result in energy savings but can also provide a reduction of carbon footprint and reduced reliance on the utility supply.
​
References
​
-
Sustainable Energy “Choosing Among Options, Jefferson W. Tester, Elisabeth M. Drake, Michael J. Driscoll, Michael W. Golay, William A. Peters 2005
-
Take Action for the Sustainable Development Goals – United Nations Sustainable Development
-
Stoecker 1989 Design of Thermal Systems Third Edition
-
CHP Energy and Emissions Savings Calculator | US EPA
-
Gas Turbines - Products | Solar Turbines
-
Design Brief Chiller Efficiency.pdf (lbl.gov)
-
https://ember-climate.org/wp-content/uploads/2021/03/Global-Electricity-Review-2021-EU.pdf
​
About Author
Gardson Githu, PE is a Senior Mechanical Engineer and Consultant at EYP Mission Critical Facilities, Part of Ramboll.
Gardson’s experience focuses on the design and analysis of HVAC systems for commercial, industrial, and Data Center infrastructure facilities. His experience includes new facilities design, retrofit design, and mechanical systems analysis.
His project experience includes chilled water plants, thermal storage systems, fuel oil systems, and air handling systems. Gardson specialized in mechanical system energy optimization, data center risk site assessment and data center thermal mapping (computational fluid dynamic analysis).
He holds a Bachelor of Science degree in mechanical engineering from California State University Los Angeles, and a Master of Science degree in mechanical engineering with Themo-fluids option, from California State University Northridge.
He is a team member of the recently launched EYP Mission Critical Facilities, Part of Ramboll and I3 Solutions Group Sustainability Initiative to offer a practical roadmap towards a Carbon Net-Zero data center by 2030.
​
Contact Us
​
For further information about the EYP MCF, Part of Ramboll and i3 GHG Abatement Group, please email David Eisenband deisenband@eypmcfinc.com or Kerry Neville kerry.neville@i3.solutions